In this series, we’re exploring different ways in which the key aspects of blockchain technology and blockchain incentives can be used to address challenges in the mineral supply chain.
By carefully making use of the ability to tokenize real world assets, maintain an unchangeable record of transactions of these assets, and create a self-governing inventive model that lets companies transact without a trusted third party, we can create an infrastructure to ensure the provenance of our raw materials.
In the last post we looked at the first aspect, tokenizing real world assets, and how to use these tokens to build up the technology in scenarios where we had a lot of implicit trust between the supply chain actors.
Now let’s look at the aspect of the unchangeable record of transactions, more specifically, what we need to do to make the best use of this.
Immutability.
One of blockchain’s biggest selling points is how difficult it is to modify information that has been entered into the system.
Blockchains rely on having copies of data resting on every participating computer, or node, who all vote on the true version of the data. This makes the data very secure, so long as a malicious actor doesn’t take control of more than 50% of the nodes.
By building on Ethereum, for example, this becomes practically impossible as there are thousands of Ethereum nodes, and only a small amount of them care enough about our supply chain tracking token that they might attempt to conspire to change the record.
This immutable record gives us confidence that the chain of custody is unbroken and accurate. This leads us to an important question: we may be sure the data is unchanged, but how do we know that the metal we receive is the metal the token is referring to?
It is not enough to have an unbroken chain of custody of the tokens, we must also have confidence that the data in the tokens that identifies the metal is unchanged.
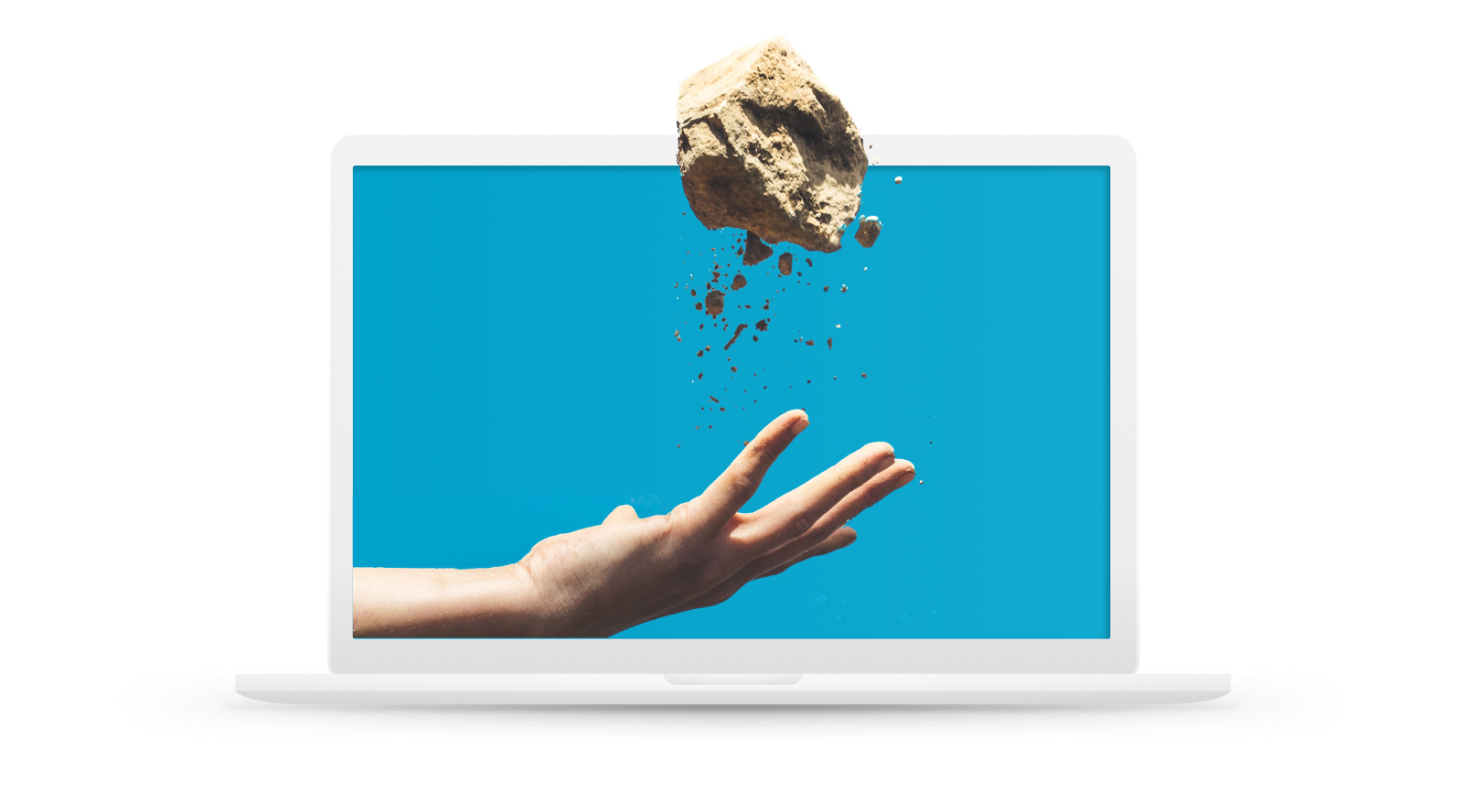
Making Use of Immutability.
Linking materials to tokens
This is the most common question people ask when they think about supply chain solutions.
How do you make sure the materials you are tracking match the records, certificates or tokens on the blockchain?
This is important for physical chain-of-custody. For implementation there are two functions we need to be able to perform:
- If we have a shipment of material, we should be able to locate the blockchain token that shows us the record of ownership and associated due diligence data.
- If we have a token we want to be able to identify and verify which shipment it relates to.
To accomplish the first task, we need to have a tag with a unique identifier that links to the blockchain.
To accomplish the second, we need information about the material stored with the token, including identifying marks, last known location, and total mass and grade tracked by the token.
Example 1
We have an ingot of tin. On the ingot is a sticker with a QR code. We scan the QR code and an app calls up our non-fungible token, which shows us the previous owners.
Example 2
We have a token for a pallet of tin ingots displayed in an app. Along with the token, the app has information about which warehouse the tin is stored in, how many ingots in the pallet, a unique identifier, and a photo of what it looks like. We can then go to the warehouse and locate the pallet.
The method we use to link the material with the token can vary depending on which problems we are trying to solve.
For example:
We may have concerns that minerals from illicit sources are being mixed in with our shipments before the minerals are processed into metal. Minerals look like piles of rocks, so if this is a concern, we might weigh the shipment before and after transport and spray the minerals with an identifying compound such as a rare radioactive isotope.
We may have concerns that tracked metal ingots in our supply chain are being lost, and that companies are replacing the ingots with fakes that have the same (forged) ID number. If this is our concern, we might take high-resolution photographs of the ingots that show fine detailed cracks and lines in the metal to prove the bar is genuine.
The important thing is that the token tracking system is flexible enough to accommodate different identification methods. This will ensure the system can adapt to the different challenges of different minerals at different stages of the supply chain.
The Necessity of Mass-balance for Processing.
Minerals and metals are raw materials, not end products by themselves. They need to be processed to be useful. Ores need to be smelted into metal. Metals need to be refined and alloyed to become useful in our end products.
Most smelters and refiners use a continuous process where ores from many sources are processed together. These processes make batch-by-batch tracing unfeasible. The world of the future may be one where all these processes are handled batch-by-batch, but for the time being, we need another way to trace beyond these processing points in the supply chain.
In order to overcome these points of processing, we can use a mass-balance approach.
The concept of mass-balance traceability is that at processing points we track volumes of material going into the process and the volumes coming out, rather than tracking the metals themselves.
For example:
A smelter purchases five 1-ton shipments of tin, 1 ton from Mine A and 4 from Mine B. These mines are both tracked, and the smelter receives tokens from both. After processing we create a new token representing the tin ingots that is linked to all the old tokens.
In this way, we consider all the tin to be 20% from Mine A and 80% from Mine B, with a link to the due diligence information from both mines. This also allows us to claim that the money paid for the ingots is traceable, 20% to Mine A and 80% to Mine B.
It is unreasonable to expect every mine to adopt a blockchain traceability system overnight. How can we deal with smelters using material from a combination of blockchain-tracked and non-blockchain sources?
In this case, we can create non-fungible tokens at the smelter level, linked to due diligence data that the smelter has performed on their mines. These tokens would not give the same level of visibility as the tokens generated at the mine, but would allow customers the choice of what to purchase.
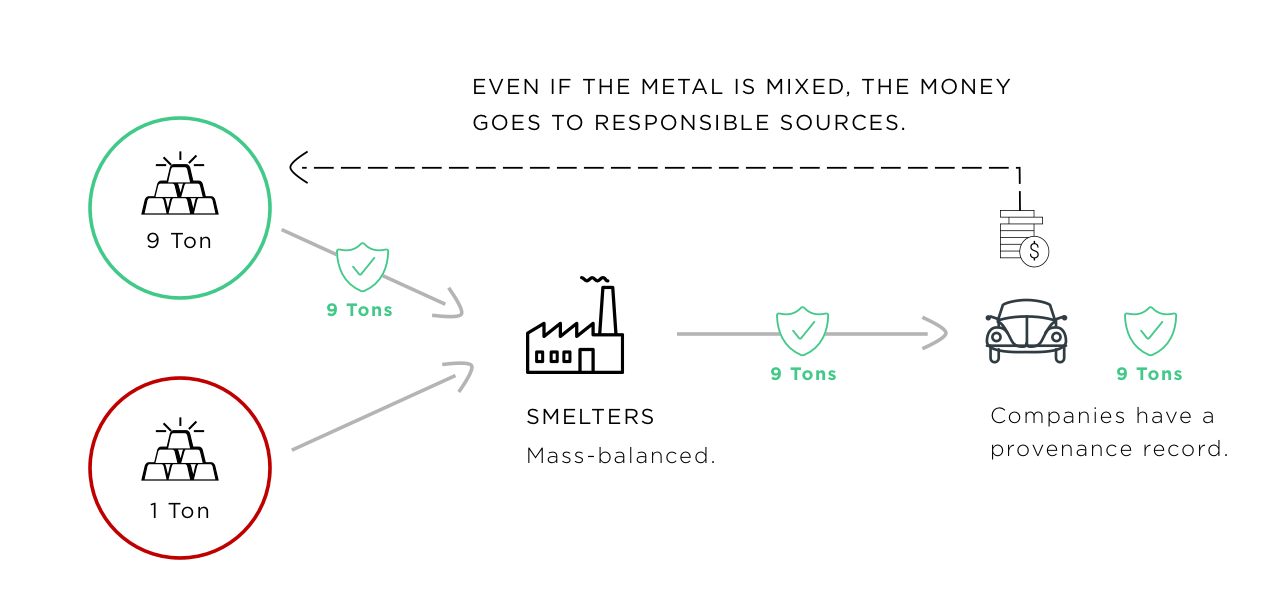
In the figure above we can see a smelter that has purchased ten tons of material but only 9 from blockchain-tracked mines. After processing, their customer wishes to purchase 9 tons of blockchain-tracked metal. The smelter then sends 9 tons of metal that has been mixed together from both sources, however, by including the 9 tons of blockchain-tracked certificates, the customer is able to know their money went to the blockchain-registered sources.
Avoiding Greenwashing.
Regardless of whether all of a smelter’s input mines are using blockchain or not, it is important that they are all responsible. We do not want blockchain-based mineral traceability to be a vector for greenwashing.
It is not enough for a smelter to purchase 50% from responsible blockchain-registered sources, and the other 50% from known conflict sources, selling their blockchain traceability tokens to downstream customers who care about traceability, and anonymous material to everyone else.
This could provide a false sense of confidence to downstream companies that they are not the ones contributing to illicit activities, reduce pressure on negative actors in the supply chain, and ultimately make on-the-ground impacts worse than not using blockchain at all.
To avoid this, it is important that the smelters continue to perform their due diligence on their input mines, as the OECD guidelines require, and encourage more and more mines to register on the blockchain over time. Blockchain tokens should be created at the smelter level, along with the associated due diligence that the smelter has done to account for any material from sources not already blockchain-enabled.
In the example above, the smelter purchased 10 tons of material, 9 of which came with non-fungible tokens that allow us to trace all the way back to the mine of origin. For the 1 ton outstanding, a token should be created at the smelter level, linked to the due diligence the smelter has performed.
Customers purchasing that material would be aware the token has not come from the mine of origin but would still have some level of trust and information on the material, and leverage for pushing the mines to adopt traceability going forward.
Could we go one step further?
Although chain-of-custody is what comes to mind most readily when we think of supply chain assurance, there are other approaches.
What if we had no link at all between the blockchain and the physical materials? Rather than tracking shipments of the material themselves as they move down the supply chain from source to manufacturer, we could track companies and the flows of material in general in and out of them with no direct link to a token or digital twin.
This approach would not allow companies to identify the provenance of any particular mass of material but instead would allow companies with long-standing supplier relationships to identify risk points in their supply chain on a company basis.
This may be sufficient for specific materials or scenarios where the concern is more about documenting company data and processes along the chain, rather than ensuring material from conflict areas is not laundered into the system. A system like this would be designed very differently than a tokenized system, so we will not cover it in detail.
By designing the technology carefully we can tie a great deal of data to minerals as they move through the supply chain. But our journey doesn’t end here. A well-designed system of tokenized metal, tied to due diligence data with a solid linkage between the digital and physical world is still only half of the story.
We still need to convince the supply chain participants to use it, which we will cover in our upcoming posts about incentives.