What is a Circular Supply Chain?
Circular supply chains are transforming traditional businesses into efficient, zero-waste systems that create new opportunities and reduce carbon emissions.
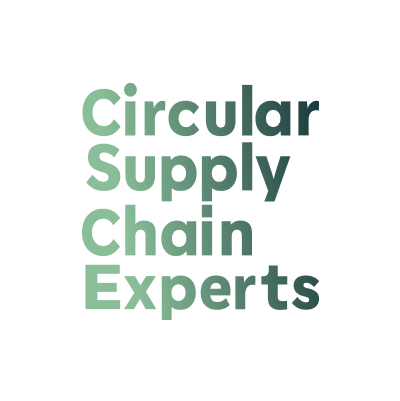
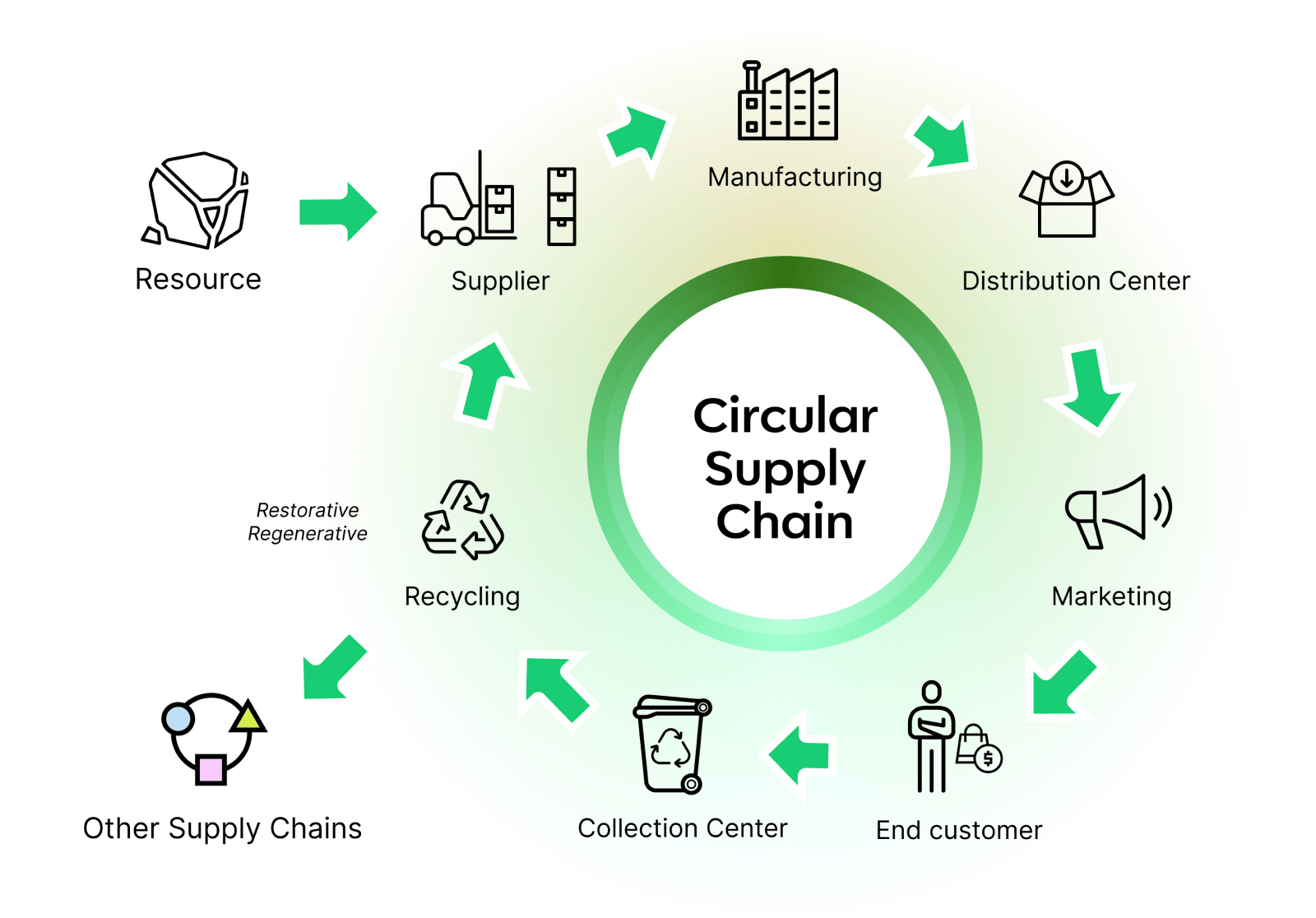
The circular economy is gaining momentum – rapidly shifting the paradigm from one-time consumption to reuse, recycling, and giving a second life to products. This presents many unique opportunities, but at the same time brings new questions: how can we enable a circular economy? How should our production processes and operations change? What is the role of data in circular supply chains and how should we reinvent ways we deal with it – how best to collect, transfer, and analyze it? All these questions are important, so we decided to dive deeper and create a series of articles about the circular economy. We’ll start from the beginning: in this article, we will explore what a circular supply chain is.
How did the circular economy evolve?
Supply chains contribute to over 80% of carbon emissions in a typical consumer goods company. At a certain point, governments and companies around the world have realized that they have to create more sustainable supply chains, and reduce their carbon footprint and overall effects on climate change.
The earliest developments of the circular economy started in the 1960s. Among some of the first notable works, was Kenneth Boulding's The Economics of the Coming Spaceship Earth. It formulated some principles that became the foundation for a circular economy. In particular, Kenneth argued that the earth is a single “spaceship” with limited resources thus materials have to circulate in a socio-economic system as long as possible.
In the 1970s, economists referred to loops and cycles while describing economic terms, processes, and resources, and in the early 2000s, some countries started implementing circular economy principles to reduce waste and enhance resource efficiency. Among some of these are:
- In China, the circular economy concept was introduced in 2002 within the 16th NCCCP (National Congress of the Chinese Communist Party) making the country one of the earliest adopters of this principle. Later, “The Circular Economy Promotion Law” (CEPL) was published and came into effect in 2008 and 2009 respectively, with a focus on 3R strategies (Reduce, Reuse, Recycle). The earliest regulations in China were focused on resource productivity.
- Another remarkable example of early circular economy initiatives on the government level is the UK with its National Industrial Symbiosis Programme (NISP) introduced in 2005. The document was focused on resource use optimisation and extension of materials life cycles.
- The Japan’s Law for Promotion of Effective Utilization of Resources established regulations that support recycling and the use of recycled materials in production processes in the early 2000s.
In short, the circular economy is an economic model that promotes the use of resources for as long as possible.
A supply chain vs. a circular supply chain
The circular supply chain is a vital part of the concept. What is different about the circular supply chain? A typical or linear supply chain presents the network of all the individuals, organizations, resources, activities and technology involved in the creation and sale of a product. The created good only travels in one direction. In contrast, circular supply chains are networks that exchange goods in different directions by transferring already created materials and reusing and recycling them. Such materials may include plastic, mineral or metal, paper, glass, and other goods.
What are the main characteristics of the circular supply chain?
Circular supply chains are revolutionizing how we think about resources and production. Unlike traditional linear models, these systems aim to reduce how much is needed from the planet, then to keep materials in use for as long as possible.
Circular supply chains are physically shorter. They focus more on repairing than building new ones. They source materials from other supply chains or renewable sources. All of this means creating interconnected systems that share data about materials to extend their lifespan.
One of the most interesting aspects is how circular supply chains turn waste into opportunity. Instead of generating waste streams, they work to eliminate them or find ways to monetize them through new customers. This shift can transform supply chains from cost centers into additional revenue streams.
Examples of circular supply chains in action are popping up across industries. Take Stellantis, the automotive giant, which has embraced the concept with its certified pre-owned parts program. This not only reduces waste but also creates a new market for used components.
Circular supply chains aim to use resources more efficiently by reducing the input of virgin materials and increasing the use of recycled or renewable materials. This involves optimizing resource use at every stage of the product life cycle.
A circular supply chain is an approach to manage and minimize waste, make the most of resources, and create sustainable systems by closing the loop on product life cycles.
A circular supply chain has several factors to consider. First and foremost, is starting with design for longevity and recycling. Product design from the outset with their end-of-life in mind. This includes considering how materials can be reused, disassembled, repaired or recycled. Design strategies may involve using modular components, non-toxic materials, and standardized parts that facilitate easy disassembly and recycling. In apparel this is done through programs that encourage resale or repair like Patagonia’s Worn Wear including DIY (Do It Yourself) videos on repair techniques.
Circular supply chains aim to use resources more efficiently by reducing the input of virgin materials and increasing the use of recycled or renewable materials. This involves optimizing resource use at every stage of the product life cycle. To support transitions, The Ellen MacArthur Foundation promotes the use of circular design principles to optimize the use of resources and minimize waste in production processes.
In a closed-loop system, products are designed to be returned to the manufacturer or a recycling facility at the end of their useful life. These products can then be dismantled, and their components can be reused or recycled into new products. I like to call it little circles and big circles depending on the steps of the loop. Mechanical recycling of fibers from mill waste is a little circle, while chemical recycling of post-consumer garments is a more complex large circle. Regardless, we need to start at some point and little circles can have impact, often leading to big circles.
A circular battery supply chain
Circularity is important for a number of industries, including EV battery supply chain.
A battery supply chain is known for its complexity and usage of critical minerals. Batteries, especially lithium-ion batteries, require specific minerals such as lithium, cobalt, nickel, graphite, and manganese. These minerals are limited, but the good news is that some of them can be reused, so governments around the world introduce regulations that require recycling and reusing critical minerals and extend their life cycle. Good examples of that are the Critical Raw Materials Act (CRMA) and the EU Battery Regulation.
A circular supply chain is vital for the lithium-ion battery industry, especially in Europe. By promoting a circular economy through the EU Battery Regulation, advancements in recycling technologies are being fostered. Advanced recycling methods efficiently extract valuable materials from spent batteries, reducing the reliance on virgin mining.
These circular practices not only align with the European Union's sustainability goals but also contribute to a more resource-efficient and competitive industry. Microvast strongly identifies with the above values, regulations and principles.
Establishing recycling practices can significantly reduce reliance on newly mined materials. Some experts estimate that recycling could meet up to 60% of market demand for critical minerals like lithium and cobalt. Besides, circular supply chains will lower environmental effects while reducing costs and boosting resource efficiency, enhancing supply chain resistance and creating new business opportunities.
Collaboration among OEMs, suppliers, recyclers, and policymakers is critical to this system, enabling closed-loop practices such as take-back programs, data sharing for traceability, and regulatory frameworks that support sustainability. In essence, circularity for the battery supply chain is about transforming our business models and supply chain practices to prioritize sustainability at every step.
Circularity in the battery supply chain means reshaping how we design, manufacture, use, and recover batteries to maximize their lifecycle and reduce environmental impact. It's not just about recycling but creating a fully integrated, closed-loop system that influences every stage of the battery life cycle.
Circularity begins with designing for modularity, allowing easy upgrades, repairs, and disassembly, which extends battery life and simplifies recycling. OEMs play a key role in pushing for designs that consider end-of-life from the start, ensuring more efficient material recovery. When a battery’s capacity falls below the required automotive standards, it can be repurposed such as by remanufacturing or for stationary energy storage, delaying the need for recycling. At the end of its useful life, the battery is responsibly recycled, recovering key materials like lithium, cobalt, nickel, graphene to be reintroduced into new production cycles, thereby reducing reliance on virgin resources.
Defining a circular supply chain in the battery field involves creating an integrated system where each stage of a battery's life is optimized for sustainability. Collaboration among OEMs, suppliers, recyclers, and policymakers is critical to this system, enabling closed-loop practices such as take-back programs, data sharing for traceability, and regulatory frameworks that support sustainability. In essence, circularity for the battery supply chain is about transforming our business models and supply chain practices to prioritize sustainability at every step. It's a holistic approach that requires us to rethink product design, material sourcing, manufacturing, and end-of-life management to create value both environmentally and economically.
Circular supply chain in figures
- The transition to a circular economy is projected to represent a $4.5 trillion opportunity by 2030.
- A survey conducted by Gartner revealed that 74% of supply chain leaders expect their profits to increase due to implementing circular economy principles by 2025.
- The Circle Economy’s Circularity Gap report stated that only 7.2% of the global economy is in 2023.
- The European Commission estimates that a circular economy could create up to 700,000 new jobs in the EU by 2030. Other estimates suggest that the circular economy will create up to 6 million jobs globally by 2030, in particular, in such areas as sustainability.
- The ultimate aim of a circular supply chain is to produce zero waste by systematically restoring and reusing industrial and natural resources.
In our next article, we will dive deeper into circular supply chain examples, challenges and solutions.
What is Circular Supply Chains Experts?
Responsible, compliant and circular supply chains are no longer a trend, this is fast becoming a must.
Minespider launched “Circular Supply Chains Experts” to track all important changes in the industry with the help of the world's top experts responsible practices, circularity, and traceability for supply chains.
Experts commentaries